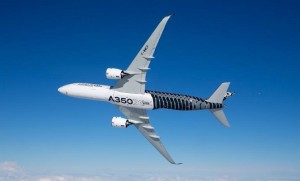
A University of Queensland PhD student has worked on a new process that allows carbon-epoxy composite materials to be welded by incorporating a thin layer of weldable material during the manufacturing process.
The process has been adopted by Airbus which is a partner in Co-Operative Research Centre for Advanced Composite Structures (CRC-ACS), and which developed and patented the ‘Thermoset Composite Welding’ technique for implementation in aircraft construction.
“More than 50 per cent of the new Airbus A350XWB structure, including the fuselage and wings, is made from composite materials,” student Luigi Vandi said in a statement. “Composite materials have become the material of choice for modern aircraft structures. This new process can significantly reduce the assembly time for aircraft made from composite materials – and consequently the cost. Using this process, welding composite materials takes only 15 minutes, compared to a typical two-hour process for conventional adhesive bonding methods.”
Vandi’s work has seen him awarded the annual ‘Early Career Researchers’ showcase prize at the CRC Association Annual Conference ‘Innovating with Asia 2014’.